Alpha Manufacturing’s CNC Punching Facilities
Our punch offering comprises of a combination of cutting edge Trumpf and Pullmax machines. Thanks to consistent significant investment in this department in recent years, we now boast one of the most advanced CNC punching services in the UK.
Trumpf TruPunch 5000s12
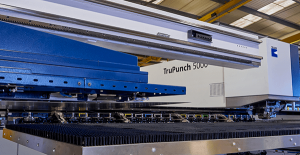
The newest of our CNC punch machines, the TruPunch 5000s12 is the fastest machine on the market with unbeatable productivity and reliability. Installed mid-2017, it is equipped with an automated Sheet Master which loads and unloads material and finished parts automatically, increasing processing speed and efficiency. Similarly, a 90-station automated tool station removes the need for manual tool changes by operators, further increasing production speed.
Trumpf Trupunch 5000
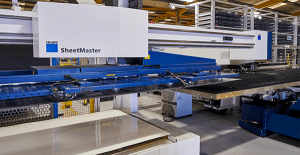
Our second TruPunch 5000 machine is also equipped with an automated Sheet Master and tool changer and in addition, is integrated into our STOPA storage system. This allows for raw material to be fed directly into the processing machine from storage and finished parts to be placed back into storage once processing is complete. This further increases processing speed and efficiency as minimal manual WIP is required during the punching process.
Pullmax 720
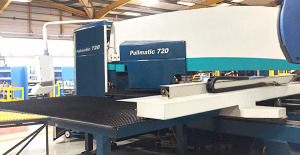
Our CNC punching department boasts two of these highly reliable, efficient Pullmax machines. These, combined with our Trumpf machines allow us to offer a flexible and dynamic CNC punching service depending on the specific needs of individual customers.
Trumpf TruMatic 6000
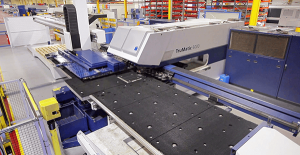
A technically advanced metal processing machine which combines laser cutting and CNC punching into a single, efficient process without the need for additional tooling. This allows for forming and profiling to be performed at once, saving time and cost for our customers. Again, an automated Sheet Master and tool changer further increase efficiency and processing speed.